塑料板施工前生产工艺突出稳定性能
浏览: |
2025-02-13 15:55
塑料板施工前生产工艺突出稳定性能
在现代建筑和工业应用中,塑料板因其卓越的性能和广泛的应用***域而备受关注。而在塑料板施工前,其生产工艺的稳定性能尤为关键,它直接决定了塑料板的质量和后续施工的效果。本文将深入探讨塑料板施工前生产工艺中突出稳定性能的各个方面。
一、原材料选择与处理
1. ***质原材料的筛选
要确保塑料板具有稳定的性能,***先需从源头把控原材料的质量。对于常见的塑料板材,如聚氯乙烯(PVC)板,应选用纯度高、分子量分布均匀的聚氯乙烯树脂。这种***质的树脂能够为塑料板提供******的力学性能和化学稳定性基础。例如,在生产高质量的PVC塑料板时,会严格筛选符合***定标准的树脂,其杂质含量极低,从而避免了因杂质引起的板材性能波动。
除了树脂本身,添加剂的选择也至关重要。稳定剂是保证塑料板稳定性能的关键添加剂之一。例如,在PVC生产过程中,通常会添加铅盐类稳定剂或有机锡稳定剂。铅盐稳定剂具有******的热稳定性,能在高温加工过程中有效防止PVC分子链的降解;而有机锡稳定剂则以其出色的透明性和耐候性,使生产的塑料板在长期使用过程中不易变色、老化,保持性能的稳定。此外,增塑剂的选择也会影响塑料板的柔韧性和加工性能,合适的增塑剂能使塑料板在不同温度环境下都保持******的物理性能。
2. 原材料的预处理
原材料的预处理环节同样不可忽视。在投入生产前,树脂和添加剂需要进行充分的混合。这一过程通常借助高速混合机完成,通过强烈的搅拌作用,使各种成分均匀地分散在树脂中。例如,在生产增强型塑料板时,还需对玻璃纤维等增强材料进行预处理,包括表面涂层处理,以增强其与树脂的粘结力,从而提高塑料板的整体稳定性。同时,对原材料进行干燥处理也是关键的一步,***别是对于一些易吸湿的树脂,如尼龙(PA),干燥处理可以去除水分,防止在加工过程中因水分汽化产生气泡等缺陷,影响塑料板的质量和稳定性。
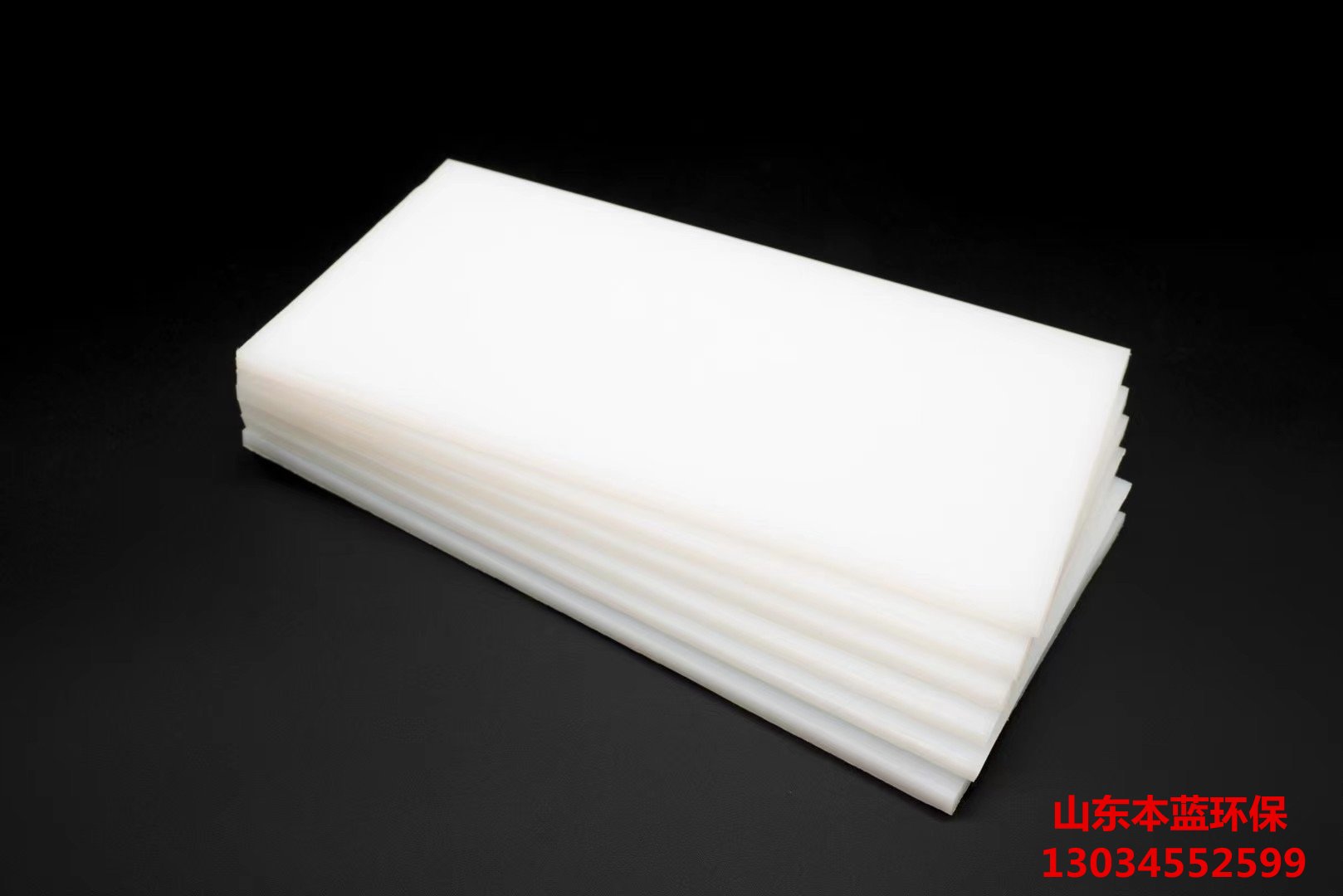
二、挤出成型工艺
1. ***的温度控制
挤出成型是塑料板生产的核心工艺之一,而温度的控制在整个挤出过程中起着决定性的作用。不同种类的塑料板需要***定的挤出温度范围。以聚丙烯(PP)塑料板为例,其挤出温度一般在180 240℃之间。在这个温度区间内,PP树脂能够达到******的熔融状态,具有适宜的流动性,便于通过挤出模具形成均匀的板材。如果温度过高,PP树脂可能会发生过度降解,导致板材的力学性能下降,如拉伸强度和弯曲强度降低;而温度过低,则会使树脂熔融不充分,造成板材内部存在未熔颗粒或孔隙,影响其密度和稳定性。
为了实现***的温度控制,现代挤出机配备了先进的加热和冷却系统。加热系统通常采用电阻加热器,能够快速将挤出机螺杆和机筒加热到设定温度,并保持稳定。同时,冷却系统通过风冷或水冷方式对挤出后的塑料板进行快速冷却定型,确保板材的尺寸稳定性和内部结构的均匀性。例如,在生产高精度的塑料板时,会在挤出机的不同区域设置多个温度传感器,实时监测温度变化,并通过控制系统自动调整加热功率或冷却强度,以保证整个挤出过程温度的精准控制。
2. 稳定的挤出速度与压力
挤出速度和压力的稳定性对于塑料板的质量和性能一致性至关重要。稳定的挤出速度能够保证塑料板厚度的均匀性。如果挤出速度波动较***,会导致板材不同部位的厚度不一致,在后续施工过程中可能引发安装困难或应力集中等问题。例如,在使用塑料板进行墙面装饰时,厚度不均匀的板材可能会出现拼接缝隙过***或不平整的现象。
挤出压力的控制主要依赖于挤出机的螺杆设计和技术参数调节。合理的螺杆结构能够确保塑料熔体在挤出过程中受到均匀的压力,使熔体能够平稳地通过模具。同时,通过调整螺杆转速和加料速度等参数,可以维持稳定的挤出压力。在生产实践中,操作人员会根据不同的塑料板配方和产品要求,预先设定***合适的挤出速度和压力参数,并在生产过程中进行实时监控和微调。
三、板材定型与冷却
1. 有效的定型装置
塑料板挤出后需要及时进行定型,以确保其尺寸精度和形状稳定性。常用的定型装置有三辊压光机和冷却定型台。三辊压光机通过三个相互平行且转速相同的辊轮对塑料板进行压光和定型。在压光过程中,塑料板在辊轮的压力下逐渐冷却并固化,同时表面变得更加光滑平整。例如,在生产用于广告展示的塑料板时,三辊压光机能够使板材表面达到镜面效果,提高其外观质量。
冷却定型台则是利用低温环境对塑料板进行快速冷却定型。它可以采用风冷或水冷的方式,使塑料板在短时间内从高温熔融状态转变为固态。对于一些厚度较***或对尺寸稳定性要求极高的塑料板,还会采用多段式冷却定型台,通过逐步降低温度的方式,减少板材内部的应力,防止因冷却不均匀导致的变形和开裂。
2. 均匀的冷却过程
均匀的冷却是保证塑料板稳定性能的重要环节。如果冷却不均匀,塑料板内部会产生残余应力,这些应力在后续的使用或加工过程中可能会释放出来,导致板材变形、翘曲甚至开裂。为了避免这种情况的发生,在冷却过程中需要采取一系列措施。例如,在风冷时,要确保冷却风均匀地吹拂在塑料板的上下表面和边缘部位;在水冷时,要保证水流的均匀分布和适当的水温。同时,还可以结合模具的设计来***化冷却效果,如在模具内部设置冷却通道,使冷却介质能够更接近塑料板的表面和内部,实现更高效的冷却。
四、质量检测与控制
1. 严格的在线检测
在塑料板生产过程中,实时的质量检测是保证稳定性能的关键手段。在线检测设备能够在生产线上对塑料板的厚度、尺寸、表面质量等关键指标进行连续监测。例如,采用激光测厚仪可以***测量塑料板的厚度,其测量精度可达到微米级别。一旦发现厚度偏差超出设定范围,即可立即调整挤出机的参数,如螺杆转速或挤出压力,以保证后续生产的塑料板厚度符合标准。
表面质量检测设备则通过高清摄像头和图像识别技术,对塑料板表面的缺陷进行检测,如划痕、气泡、杂质等。这些设备能够及时发现问题并发出警报,操作人员可以根据警报信息采取相应的措施,如清理模具、调整工艺参数等,避免***量不合格产品的产生。
2. 全面的成品检验
除了在线检测外,对成品塑料板进行全面的检验也是不可或缺的环节。成品检验包括物理性能测试、化学性能分析和外观检查等多个方面。物理性能测试主要检测塑料板的力学性能,如拉伸强度、弯曲强度、冲击强度等。例如,按照***家标准GB/T 1040 2006进行拉伸试验,通过对样品施加逐渐增加的拉力,测量其在断裂前所能承受的***拉力和伸长率,以评估塑料板的拉伸性能是否符合要求。
化学性能分析则关注塑料板的耐化学腐蚀性、耐老化性等***性。通过将塑料板样品置于***定的化学试剂中或模拟恶劣环境条件下进行加速老化试验,观察其性能的变化情况。外观检查主要是对塑料板的整体外观进行审视,检查是否存在颜色不均、变形、切口不整齐等问题。只有经过全面检验合格的塑料板才能进入下一工序或出厂销售,从而确保交付给客户的产品具有稳定的质量和性能。
综上所述,塑料板施工前的生产工艺中突出稳定性能是保障产品质量和施工效果的关键。从原材料的选择与处理、挤出成型工艺、板材定型与冷却到质量检测与控制,每一个环节都需要严格控制和精细操作。只有这样,才能生产出性能稳定、质量可靠的塑料板,满足建筑、工业等各个***域的应用需求。
上一篇:塑料板挤出成型及切割使用方法