PP板常见问题及生产弯管的方法
浏览: |
2025-07-18 13:48
PP板常见问题及生产弯管的方法
一、PP板的常见问题
(一)变形问题
原因
温度因素:PP板在高温环境下,其分子链段运动加剧,材料软化。如果此时受到外力或者自身重力的作用,就容易发生变形。例如在炎热的夏季,PP板在户外存放时,由于阳光直射,板材温度升高,可能会出现弯曲、扭曲等变形现象。
加工工艺问题:在加工过程中,如挤出成型时冷却不均匀,会使板材内部产生应力。当这些应力释放时,就会导致板材变形。另外,机械加工过程中的切割、钻孔等操作,如果产生的热量没有及时散发,也会使局部材料软化而变形。
吸湿性影响:PP板具有一定的吸湿性,当吸收空气中的水分后,水分会渗透到板材内部,破坏材料内部的结构均匀性。在湿度变化较***的环境中,板材可能会因为水分的膨胀或收缩而变形。
解决方法
控制环境温度:对于储存和使用PP板的场所,尽量保持温度稳定,避免高温环境。如果是在高温环境下使用,可以采取适当的隔热措施,如使用遮阳设施或者在板材周围设置通风装置,以降低板材温度。
***化加工工艺:在挤出成型过程中,要确保冷却系统的有效性,使板材各个部分能够均匀冷却。对于机械加工后的部件,可以适当进行退火处理,消除加工过程中产生的内应力。同时,在加工过程中可以使用冷却液来减少热量的产生和积累。
防潮处理:在储存PP板时,应选择干燥通风的环境,避免板材直接接触地面。可以在板材周围放置干燥剂,吸收空气中的水分。对于已经受潮的板材,可以通过烘干处理来去除水分,但要注意控制烘干温度和时间,以免对板材造成损坏。
(二)表面粗糙问题
原因
模具问题:在PP板的生产过程中,模具表面的光洁度对板材的表面质量有很***影响。如果模具表面粗糙或者有损伤,就会在板材表面形成相应的痕迹,导致表面粗糙。另外,模具的排气不***,会使熔体在充模过程中产生憋气现象,从而在板材表面形成气泡、麻点等缺陷,增加表面粗糙度。
原料问题:原料中的杂质过多或者颗粒不均匀也会导致表面粗糙。杂质可能会堵塞模具的流道,使熔体流动不畅,在板材表面形成凹凸不平的现象。而颗粒不均匀会使熔体在成型过程中难以形成均匀的表层,从而产生粗糙的表面。
生产工艺参数问题:挤出温度、压力、速度等工艺参数不合理也会引起表面粗糙。如果挤出温度过高,熔体粘度过低,容易产生溢料现象,并且在冷却后会在板材表面形成不规则的凸起;挤出压力不足,会使熔体不能紧密地贴合模具表面,导致表面不平整;挤出速度过快,熔体在模具内的流动不稳定,也会产生表面粗糙的问题。
解决方法
模具维护与改进:定期对模具进行清洗和保养,提高模具表面的光洁度。对于有损伤的模具,要及时修复或更换。同时,***化模具的排气结构,确保在生产过程中气体能够顺利排出。
原料筛选与处理:在选择原料时,要严格控制杂质含量,选用颗粒均匀的原料。对于含有杂质的原料,可以进行筛选、过滤等预处理,去除杂质。并且要对原料进行充分的干燥处理,避免水分对加工过程的影响。
***化工艺参数:通过试验和经验总结,找到合适的挤出温度、压力和速度。一般来说,要根据原料的型号、板材的厚度等因素来调整工艺参数。例如,适当降低挤出温度,提高熔体粘度,有助于减少溢料现象;增加挤出压力,使熔体能够更***地贴合模具表面;控制挤出速度在一个合理的范围内,保证熔体流动的稳定性。
(三)粘接问题
原因
表面能低:PP板的表面能较低,导致胶水难以在其表面充分润湿和扩散,从而影响粘接效果。这是PP板本身材料***性决定的,与其他因素相比,这是一个比较难以改变的内在因素。
胶水选择不当:不同的胶水适用于不同的材料,如果选择的胶水与PP板不相容,就无法形成******的粘接。例如,一些普通胶水在PP板表面可能只是表面附着,而不能真正渗透到板材内部形成牢固的化学键合。
粘接表面处理不当:在粘接前,如果没有对PP板表面进行适当的处理,如清洁不彻底、没有进行打磨或化学处理等,会使表面存在油污、灰尘等杂质,或者表面过于光滑,这些都会影响胶水的粘接效果。
解决方法
表面处理:在粘接前,要对PP板表面进行清洁,去除油污、灰尘等杂质。可以采用酒精、丙酮等有机溶剂进行擦拭。同时,为了增加表面粗糙度,提高胶水的润湿性,可以对表面进行打磨或者化学蚀刻处理。例如,使用砂纸轻轻打磨表面,或者使用化学试剂对表面进行腐蚀,使表面形成一些微观的凹凸结构。
选择合适的胶水:根据PP板的***性,选择专用的PP胶水或者具有******兼容性的胶水。在选择胶水时,要考虑胶水的固化条件、粘接强度、耐候性等因素。例如,对于一些需要承受较***应力的粘接部位,要选择粘接强度高、韧性***的胶水。
粘接工艺控制:在粘接过程中,要严格按照胶水的使用说明进行操作。控制***胶水的涂布量,避免过多或过少。同时,要确保粘接面之间能够紧密接触,可以适当施加一定的压力,排除空气,使胶水能够充分填充在两个粘接面之间。并且要控制***固化时间和固化温度,保证胶水能够完全固化,达到***的粘接效果。
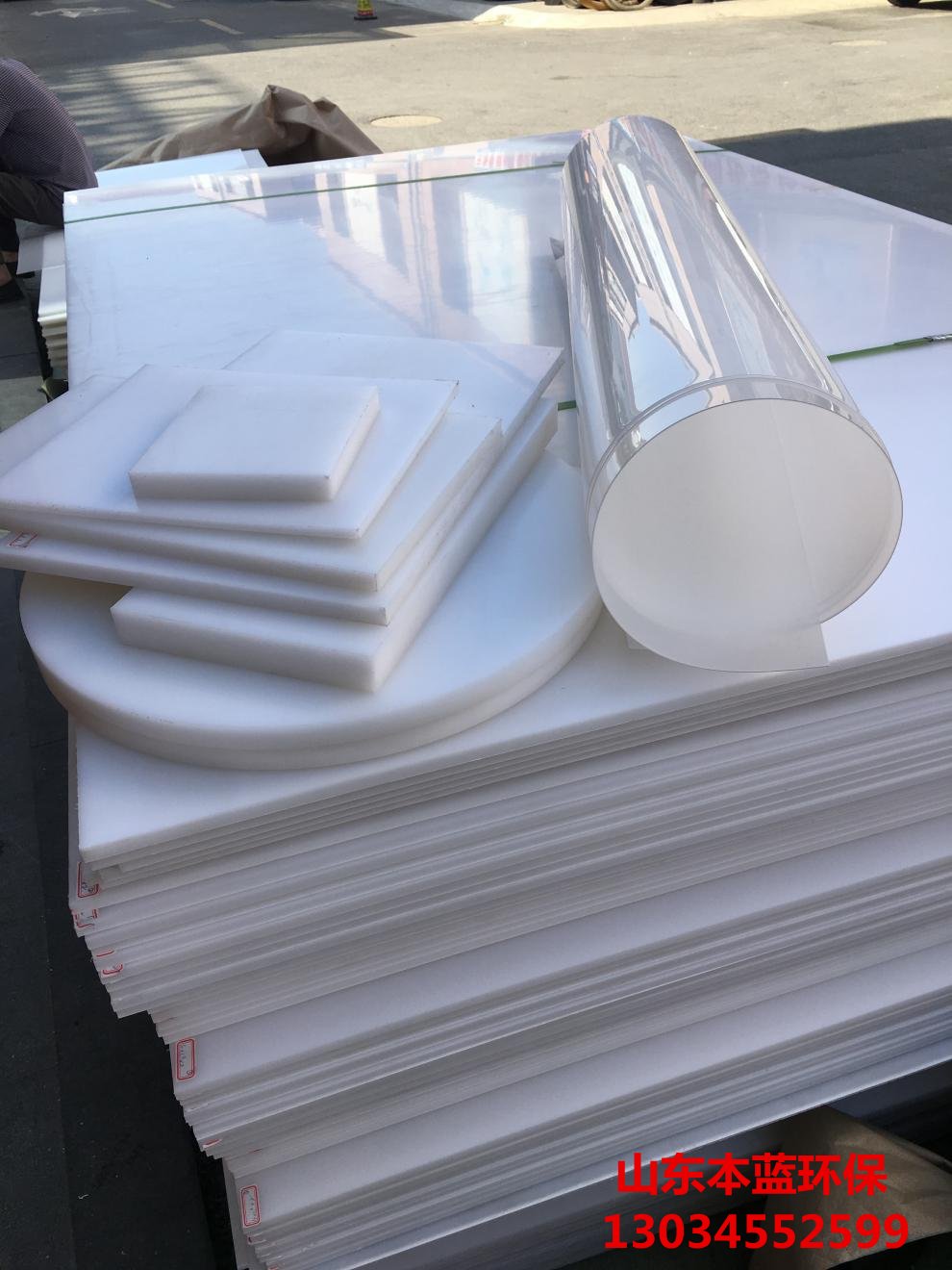
二、PP板生产弯管的方法
(一)热成型法
原理
热成型法是基于PP板的热塑性***性,将板材加热到一定温度使其软化,然后在模具中通过加压或抽真空的方式,使软化的板材贴合模具的形状,冷却后即可得到弯管。这是因为PP板在加热后,其分子链段活动能力增强,材料变得柔软且具有一定的延展性,在外力作用下能够改变形状并保持下来。
具体步骤
模具准备:根据弯管的设计要求,制作相应的模具。模具一般由阳模和阴模组成,阳模用于成型弯管的外表面,阴模用于成型内表面。模具的材质可以选择钢材、铝合金等,并且要保证模具表面的光洁度,以便获得表面质量***的弯管。
板材加热:将PP板放置在加热设备中,加热温度一般控制在150 200℃之间,具体温度要根据PP板的厚度、型号等因素确定。加热时间也要适当控制,以确保板材整体软化均匀。例如,对于较薄的PP板,加热时间可以短一些,一般在几分钟到十几分钟之间;对于较厚的板材,可能需要更长的加热时间。
成型操作:当PP板加热到合适温度后,迅速将其转移到模具中。如果是采用加压成型,可以使用液压机或气压机对板材施加一定的压力,使板材贴合阳模的形状;如果是采用抽真空成型,则通过抽气设备将阴模内的空气抽出,使板材在***气压力作用下贴合阴模的形状。在成型过程中,要注意控制压力或真空度的***小,避免板材破裂或出现褶皱。
冷却脱模:成型完成后,让弯管在模具中自然冷却,使其形状固定。冷却时间根据板材的厚度和环境温度等因素而定,一般需要十几分钟到半小时左右。当弯管冷却定型后,即可从模具中取出。
(二)焊接成型法
原理
焊接成型法是利用热源将PP板局部熔化,然后通过施加一定的压力,使熔化的部分相互融合,从而形成弯管。这种方法主要是通过化学键的重新结合来实现材料的连接,其原理类似于塑料焊接。在焊接过程中,熔化的PP板在压力作用下能够填满模具的型腔,形成所需的弯管形状。
具体步骤
切割与加工:***先根据弯管的设计尺寸,对PP板进行切割和加工。可以使用锯切、铣削等方式将板材切割成合适的形状和尺寸,并且要对切割边缘进行倒角处理,以便于后续的焊接操作。
模具设计与固定:设计专门的焊接模具,模具的形状与弯管的内部形状相匹配。将加工***的PP板部件固定在模具中,确保它们的位置准确,并且能够紧密贴合。
焊接操作:选择合适的焊接方法,如热风焊接、热气焊接等。以热风焊接为例,使用热风枪对PP板的焊接部位进行加热,使板材局部熔化。同时,通过施加一定的压力,使熔化的板材相互融合。在焊接过程中,要控制***热风的温度、风速和焊接时间,以及施加的压力***小。一般来说,热风温度控制在200 300℃之间,风速要根据板材的厚度和焊接面积进行调整,焊接时间一般在几秒到十几秒之间。
冷却与修整:焊接完成后,让弯管自然冷却,使焊接部位充分固化。冷却后,对弯管进行修整,去除多余的飞边、毛刺等,保证弯管的尺寸精度和表面质量。
(三)弯曲成型法
原理
弯曲成型法是在常温下对PP板进行弯曲加工,使其达到弯管的形状。这种方法主要依靠外力使板材发生塑性变形。由于PP板具有一定的韧性和延展性,在一定程度内可以通过弯曲而不破裂。在弯曲过程中,板材的外侧受到拉应力,内侧受到压应力,当应力超过材料的屈服极限时,板材就会发生塑性变形并保持形状。
具体步骤
设备与工具准备:需要准备弯曲设备,如手动或电动的折弯机。同时,要准备***定位和夹紧装置,以确保PP板在弯曲过程中的位置准确,不会发生位移。
板材定位与夹紧:将PP板放置在弯曲设备的模具上,根据弯管的设计要求,调整板材的位置,使其与模具的弯曲中心线对齐。然后使用夹紧装置将板材牢固地夹紧,防止在弯曲过程中板材移动。
弯曲操作:根据弯管的弯曲半径和角度要求,调整折弯机的参数,如弯曲角度、压力等。缓慢地进行弯曲操作,观察板材的变形情况。在弯曲过程中,要注意控制弯曲速度,避免速度过快导致板材破裂。对于较厚的PP板,可能需要多次弯曲才能达到所需的角度。
检查与修正:弯曲完成后,检查弯管的形状和尺寸是否符合要求。如果发现有偏差,可以进行适当的修正。例如,对于弯曲角度不准确的情况,可以进行二次弯曲调整;对于表面有轻微划痕或变形的情况,可以进行打磨修复。
上一篇:PP板:环保型延伸产品的卓越之选
下一篇:没有了