PP板生产色差控制及废弃处理:工艺优化与环保实
浏览: |
2025-07-01 13:41
PP板生产色差控制及废弃处理:工艺***化与环保实践
在塑料加工行业中,聚丙烯(PP)板以其***异的性能,如******的化学稳定性、高强度、耐冲击性以及易于加工等***点,广泛应用于建筑、包装、广告、化工等多个***域。然而,在PP板的生产过程中,色差控制与废弃处理是两个至关重要且相互关联的环节,它们不仅直接影响产品的外观质量和市场竞争力,还关乎企业的环保责任和可持续发展。
一、PP板生产色差控制
(一)原料选择与管理
PP板的生产原料主要包括聚丙烯树脂、色母粒以及各种添加剂。为了有效控制色差,***先需确保原料的稳定性和一致性。
聚丙烯树脂:应选用同一品牌、同一型号且质量稳定的产品。不同批次的聚丙烯树脂可能会因生产工艺的微小差异而导致分子量分布、熔融指数等参数有所不同,进而影响***终产品的色泽。在采购时,要与供应商建立长期稳定的合作关系,要求其提供详细的质量检测报告,并对每批进货进行严格的检验,包括外观、熔融指数、水分含量等指标的检测,确保符合生产要求。
色母粒:色母粒是决定PP板颜色的关键因素之一。***质的色母粒应具备******的分散性、高色素含量以及稳定的色泽。在选择色母粒时,要根据所需颜色进行***匹配,并考虑其与聚丙烯树脂的相容性。同时,要对色母粒的生产厂家进行严格筛选,要求其生产过程遵循严格的质量控制标准,保证每批色母粒的色泽一致性。在储存过程中,色母粒应存放在干燥、通风、避光的环境中,防止因受潮、光照等因素导致颜色变化。
添加剂:除了色母粒外,PP板的生产过程中还可能添加抗氧剂、润滑剂等添加剂。这些添加剂的选择和使用量也会对产品的色泽产生一定影响。因此,在配方设计时,要充分考虑添加剂与聚丙烯树脂和色母粒之间的相互作用,通过试验确定***的添加剂种类和用量,以确保产品颜色的稳定。
(二)生产工艺控制
1. 混料过程
混料是PP板生产的***步,其目的是将聚丙烯树脂、色母粒以及各种添加剂均匀混合。在混料过程中,要严格控制混料的时间、温度和转速等参数。
时间:混料时间过短,可能导致原料混合不均匀,出现色差;混料时间过长,则可能引起原料的过热分解,影响产品性能和色泽。一般来说,根据不同的原料配方和混料设备,混料时间应控制在5 15分钟之间。在实际操作中,可通过观察混料后的物料颜色是否均匀一致来判断混料时间是否合适。
温度:混料温度的控制也至关重要。温度过低,原料的流动性差,不利于均匀混合;温度过高,则可能加速原料的化学反应,导致颜色变化。通常,混料温度应控制在聚丙烯树脂的熔融温度以下10 20℃范围内,具体温度可根据原料的具体情况进行调整。
转速:合理的混料转速能够保证原料在混料过程中充分混合。转速过低,混料效果不佳;转速过高,则可能使物料过度摩擦生热,影响产品质量。一般情况下,混料转速应根据混料设备的型号和容量进行适当调整,以确保物料在混料过程中能够均匀翻滚,达到******的混合效果。
2. 挤出成型过程
挤出成型是PP板生产的核心环节,对产品的颜色和质量有着决定性影响。
挤出温度:挤出温度的控制直接影响PP板的塑化效果和颜色稳定性。如果挤出温度过低,聚丙烯树脂的塑化不完全,会导致产品表面粗糙、光泽度差,同时也可能使色母粒分散不均匀,产生色差;而挤出温度过高,则可能引起聚丙烯树脂的分解变色,使产品颜色变深甚至出现焦烧现象。因此,在挤出成型过程中,要根据聚丙烯树脂的熔融指数、色母粒的***性以及产品的厚度等因素,合理设置挤出机各段的温度。一般来说,机筒温度应从加料口到机头逐渐升高,形成一个合理的温度梯度,以利于物料的塑化和挤出。
螺杆转速:螺杆转速不仅影响PP板的生产效率,还会对产品的颜色和质量产生影响。转速过低,物料在机筒内的停留时间过长,容易发生分解变色;转速过高,则可能导致物料塑化不***,出现熔体破裂等现象,同时也会使机筒内压力增***,影响色母粒的分散效果。因此,在生产过程中,要根据挤出机的型号、机筒温度以及产品的规格等因素,选择合适的螺杆转速,并通过实际生产中的观察和调整,找到***的工艺参数组合。
模具结构与温度:模具的结构设计合理与否直接影响PP板的成型质量和颜色均匀性。模具的流道应尽量光滑、流畅,避免出现死角和物料滞留现象,以防止色母粒在局部堆积而产生色差。此外,模具温度的控制也很重要。模具温度过低,会使PP板的冷却速度过快,导致表面光泽度差、内应力***;模具温度过高,则可能使产品出现翘曲变形等问题。因此,在生产过程中,要根据产品的厚度和材质,合理设置模具温度,并通过冷却系统对模具进行***控温。
3. 牵引与切割过程
牵引速度和切割精度也会对PP板的颜色产生一定影响。
牵引速度:牵引速度应与挤出速度相匹配,以保证PP板的尺寸稳定性和平整度。如果牵引速度过快,会使PP板在牵引过程中受到过***的拉伸应力,导致产品厚度不均匀、表面出现划痕等问题,同时也可能使颜色发生变化;牵引速度过慢,则会使PP板在冷却过程中产生较***的内应力,影响产品的尺寸精度和物理性能。因此,在生产过程中,要根据挤出机的出料速度和产品的要求,合理调整牵引速度,并通过在线监测设备对产品的尺寸和厚度进行实时监控,确保产品质量稳定。
切割精度:切割过程中产生的切口应平整、光滑,避免出现毛刺和碎屑。如果切割精度不高,切口处可能会出现颜色变化或局部烧焦现象,影响产品的外观质量。因此,要定期对切割刀具进行检查和更换,确保刀具的锋利度和切割精度。同时,在切割过程中,要注意调整切割参数,如切割速度、切割压力等,以减少切割过程中产生的热量对产品颜色的影响。
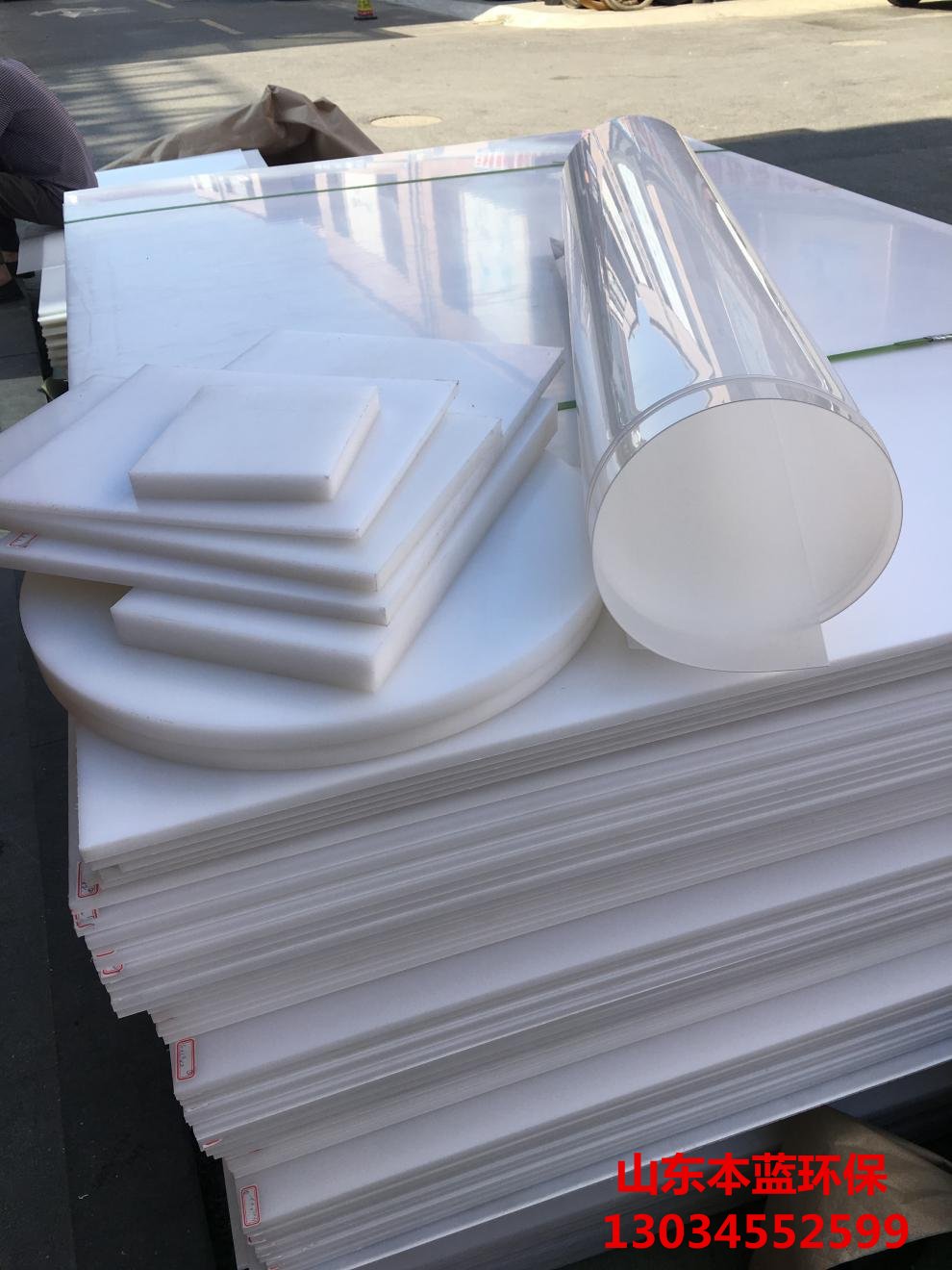
(三)质量检测与反馈
为了确保PP板产品的颜色一致性,在生产过程中要建立完善的质量检测体系,并对检测结果进行及时反馈和处理。
在线检测:在挤出成型过程中,可安装在线测色仪对PP板的颜色进行实时监测。测色仪能够快速、准确地测量产品的色差值,并将数据传输至控制系统。一旦发现色差超出设定范围,系统能够及时发出警报,提醒操作人员进行调整。同时,操作人员也可以通过观察产品的外观颜色,与标准样品进行对比,及时发现颜色异常情况并采取相应措施。
离线检测:除了在线检测外,还需要对生产出的PP板进行定期的离线检测。离线检测主要包括对产品的色泽、光泽度、厚度等指标的检测。通过对***量样品的检测和数据分析,可以进一步了解产品的颜色稳定性和质量状况,为生产工艺的***化和调整提供依据。
反馈与调整:当检测到色差问题时,要及时将信息反馈至生产部门,以便对生产工艺进行调整。调整措施可能包括对原料配方的微调、挤出机温度和螺杆转速的改变、模具温度的调整等。同时,要对调整后的产品进行再次检测,确保色差问题得到有效解决。此外,还要建立质量追溯机制,对出现色差问题的产品的生产过程进行详细记录和分析,以便找出问题的根源,防止类似问题再次发生。
二、PP板废弃处理
(一)废弃PP板的来源与分类
PP板在生产过程中以及使用后都会产生一定量的废弃物。生产过程中的废弃物主要包括边角料、废料、不合格品等;使用后的废弃物则主要来源于PP板制品的报废,如旧的建筑模板、广告牌、包装材料等。
根据废弃PP板的来源和污染程度,可将其分为两类:一类是未经使用或稍微沾染杂质的干净废弃PP板,如生产过程中的边角料和部分不合格品;另一类是使用后受到严重污染的废弃PP板,如沾染了油污、油漆、泥土等杂质的旧制品。
(二)废弃PP板的处理方法
1. 物理回收法
物理回收法是废弃PP板处理的主要方法之一,该方法主要通过破碎、清洗、干燥、熔融造粒等工序,将废弃PP板转化为可再利用的聚丙烯颗粒。
破碎:将废弃PP板通过破碎机破碎成较小的碎片或颗粒,以便于后续的处理。破碎过程中要注意控制破碎设备的参数,如破碎速度、破碎间隙等,以确保破碎后的颗粒***小均匀,有利于提高后续清洗和熔融造粒的效果。
清洗:对于受到污染的废弃PP板,需要进行清洗处理,以去除表面的杂质和污染物。清洗过程可采用水洗或溶剂清洗的方式。水洗法适用于一般污染的废弃PP板,通过加入适量的清洗剂和水,在一定的温度和搅拌条件下进行清洗,然后用清水冲洗干净;溶剂清洗法则适用于油污等难以清洗的污染物,选用合适的有机溶剂对废弃PP板进行浸泡和清洗,但要注意溶剂的回收和处理,避免对环境造成二次污染。
干燥:清洗后的废弃PP板含有一定量的水分,需要通过干燥设备进行干燥处理,以去除水分。干燥温度和时间应根据废弃PP板的厚度和含水量进行合理调整,一般干燥温度控制在80 100℃之间,干燥时间约为2 4小时。
熔融造粒:干燥后的废弃PP板碎片通过熔融造粒机进行熔融造粒,将其转化为可再利用的聚丙烯颗粒。在熔融造粒过程中,要控制***温度、压力和转速等参数,以确保颗粒的质量和性能。造粒后的聚丙烯颗粒可作为原料直接用于PP板的再生产,实现资源的循环利用。
2. 化学回收法
化学回收法是通过化学反应将废弃PP板中的聚丙烯分解为低分子化合物或单体,然后对这些产物进行回收和利用。目前,化学回收法主要包括催化裂解、水解和氧化降解等方法。
催化裂解:在催化剂的存在下,将废弃PP板加热至一定温度,使其发生裂解反应,生成丙烯、乙烯等小分子烯烃和少量其他气体。这些小分子烯烃可作为化工原料用于合成新的聚丙烯或其他塑料制品。催化裂解法具有反应速度快、产物收率高等***点,但催化剂的成本较高,且裂解过程中产生的气体混合物需要进一步分离和提纯,增加了回收成本和难度。
水解:利用水解反应将废弃PP板中的聚丙烯分解为低分子化合物。水解反应通常需要在酸性或碱性条件下进行,反应温度较高,且反应时间较长。水解产物主要包括丙酸、丙醇等小分子有机物,这些产物可进一步进行处理和利用,如通过蒸馏、精馏等方法进行分离和提纯,得到高纯度的化学品。然而,水解法的反应条件较为苛刻,对设备的要求较高,且水解过程中可能会产生一些难以处理的副产物,限制了其***规模应用。
氧化降解:通过氧化剂的作用,使废弃PP板中的聚丙烯发生氧化降解反应,生成二氧化碳、水和其他小分子氧化物。氧化降解法可在常温常压下进行,反应条件相对温和,但反应速度较慢,且氧化产物较为复杂,难以实现有效的回收和利用。因此,氧化降解法通常作为一种辅助处理方法,与其他回收方法相结合使用。
3. 能量回收法
对于无法通过物理回收或化学回收方法进行处理的废弃PP板,可采用能量回收法,即将其作为燃料进行燃烧,利用燃烧产生的热能进行发电或供热。能量回收法具有处理量***、成本低等***点,但燃烧过程中会产生二氧化碳、烟尘等污染物,对环境造成一定的影响。因此,在采用能量回收法处理废弃PP板时,要配套完善的污染治理设施,如废气净化系统、粉尘收集装置等,以减少污染物的排放。
(三)废弃PP板处理的环保意义与发展趋势
废弃PP板的处理不仅关系到资源的回收利用,更具有重要的环保意义。通过有效的废弃处理,可以减少废弃PP板对环境的污染,降低对自然资源的依赖,实现塑料产业的可持续发展。
随着环保意识的不断提高和法律法规的日益严格,废弃PP板的处理技术也在不断发展和完善。未来,废弃PP板的处理将朝着更加高效、环保、资源化的方向发展。一方面,物理回收法将不断***化和升级,通过改进破碎、清洗、干燥和熔融造粒等设备的技术和工艺,提高回收效率和产品质量;另一方面,化学回收法和能量回收法将与物理回收法相结合,形成综合处理技术体系,实现废弃PP板的***化利用和***小化环境污染。同时,加强对废弃PP板处理过程中的环境监管和污染防治,推动塑料产业的绿色转型和可持续发展。
综上所述,PP板的生产过程需要严格控制色差,确保产品质量的稳定性和一致性;而对于废弃PP板的处理,则要根据其来源和***点选择合适的处理方法,实现资源的循环利用和环境保护。通过在生产和废弃处理环节的共同努力,可以促进PP板行业的健康发展,为经济社会的可持续发展做出贡献。